Podział zestawów kołowych
Zestawem kołowym nazywa się zespół
złożony z osi, kół bosych, obręczy i pierścienia zaciskowego lub (w
przypadku kół monoblokowych) tylko z osi i kół. Zestaw jest zmontowany
tak, że nie ma możliwości ruchu względnego części składowych. Ma to
zarówno wady jak i zalety. Zaletą jest przede wszystkim wytrzymałość
takiej konstrukcji i jej prostota, natomiast wadą - występowanie mikropoślizgów podczas jazdy w
łukach. Jest to spowodowane tym, że koło wewnętrzne ma do pokonania
mniejszą drogę niż zewnętrzne, a stałe przymocowanie obu kół do osi
uniemożliwia ich względny ruch.
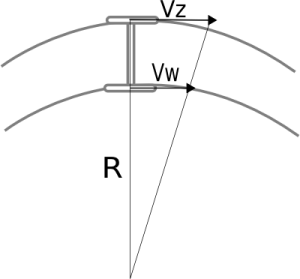
Wyjaśnienie przyczyn powstawania mikropoślizgów
zestawów kołowych w łuku
Istnieją rozwiązania konstrukcyjne z niezależnymi kołami lub kołami
obracającymi się na nieruchomej osi. Są one wykorzystane w kilku
tramwajach. Cechują się małą wytrzymałością, są skomplikowane w
produkcji i dosyć kosztowne. Zastosowano je tylko w celu zapewnienia
całkowitej niskopodłogowości pojazdu.
Ze względu na przeznaczenie zestawy kołowe możemy
podzielić na zestawy do pojazdów trakcyjnych i do wagonów.
Zestawy kołowe przeznaczone do pojazdów trakcyjnych dzielą się z kolei
na toczne i napędne. Nie są one znormalizowane. Konstruuje się je w
zależności od potrzeb dla danego pojazdu. Należy przy tym wziąć pod
uwagę sposób przeniesienia napędu na koła. Zazwyczaj służy do tego duże
koło zębate mocowane skurczowo na osi lub na wale drążonym.
Zestawy kołowe dla wagonów kolejowych składają się z części
znormalizowanych. Rodzaj zastosowanego materiału i jego obróbka
cieplna, wymiary i dokładność wykonania zależą głównie od prędkości
konstrukcyjnej, do której przewidziany jest zestaw kołowy.
Osie zestawów kołowych
Osie wytwarzane są z wlewków hutniczych,
odlewanych obecnie przede wszystkim metodą odlewania ciągłego. Wlewek taki ma kształt walca,
który jest odcinany i przekazywany do obróbki plastycznej.
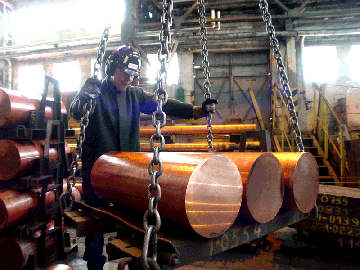
Wlewki walcowe ucięte na części do obróbki
plastycznej
Walec taki
jest następnie kuty na tzw. kęsisko celem zmniejszenia jego średnicy
(około 3-krotnie) lub bezpośrednio kuty na oś. Kucie osi odbywa się w
temperaturze powyżej 860°C i w jego wyniku otrzymuje się zgrubny
kształt osi wagonowej. Należy przy tym pamiętać o odcięciu głowy i
stopy wlewka, w których gromadzą się zanieczyszczenia i gazy podczas
odlewania.
Po obróbce plastycznej przeprowadza się obróbkę cieplną.
Osie w większości przypadków są normalizowane. Polega to na wygrzaniu
osi przez kilka godzin w temp. 850°C i studzeniu w spokojnym powietrzu
w hali. W przypadku powstania niewielkich skrzywień można jeszcze taką
oś wyprostować na gorąco i ponownie normalizować. Normalizacja stali
powoduje zmniejszenie i wyrównanie rozmiaru ziarna i ma na celu
podniesienie przede wszystkim odporności na zmęczenie.
Po obróbce plastycznej obrabia się oś mechanicznie, przez
obróbkę skrawaniem. Ze względu na rozmiary osi wykorzystywane są
specjalne tokarki.
Pierwszym etapem jest wywiercenie wstępnych nakiełków w czołach osi w
celu jej zamocowania w kłach. Następnie oś jest toczona zgrubnie.
Ostatnim etapem wykonywania osi jest obróbka mechaniczna
na wymiar. W tej fazie wykonuje się ostateczny nakiełek normalny,
wierci się i gwintuje otwory na nasadkę łożysk, planuje się czoła na
wymiar i toczy zaokrąglenia na przejściach średnic osi (zabezpiecza to
przed spętrzeniem naprężeń wywołanym zjawiskiem zmęczeniowym).
Dodatkowym wzmocnieniem osi może być wytworzenie zgniotu przez
rolowanie.
Wszystkie wymiary osi wagonowych są znormalizowane wg PN i
BN, z których najważniejsza jest norma PN-71/K-91046. Osie napędnych
zestawów kołowych są wykonywane w zależności od
sposobu przeniesienia napędu.
Oś wagonowa wraz z
najważniejszymi wymiarami (model CAD). Widoczne czoło z otworami
gwintowanymi
Istnieje kilka rodzajów osi,
z których kilka nie jest już wytwarzanych. Są to osie z końcówką
gwintowaną, na którą wkręcało się nakrętki łożyskowe. Także osie z
czopami do łożysk ślizgowych i z kołnierzem zabezpieczającym ich
panewki przed zsunięciem są wykonywane rzadko. Obecnie łożyska ślizgowe
są wykorzystywane właściwie tylko do łożyskowania oparcia silnika na
wale drążonym. Prawie wszystkie wykonywane współcześnie osie mają na
czołach otwory gwintowane, służące do przykręcenia nasadki łożysk
tocznych.
Różne osie. Od
góry: oś lokomotywy manewrowej z czopem do łożysk ślizgowych,
oś z otworami do nasadki
łożyskowej, oś zestawu SUW-2000, oś toczna do łożysk ślizgowych
Osie najczęściej wykonuje się
ze stali P35G. Jest to stal przeznaczona dla kolejnictwa, o
podwyższonej zawartości manganu. Materiały na osie wymienione są w
normie PN-84/H-84027-4.
Koła monoblokowe
Obecnie w kolejnictwie
wykonuje się prawie wyłącznie koła monoblokowe (jednoczęściowe).
Powodem tego jest niższy koszt ich wykonania, prostota (brak części
składowych) i wyższe bezpieczeństwo jazdy.
Koła takie wykonywane są z wlewków uciętych na odpowiednią
długość przez kucie na gorąco najpierw swobodne, a następnie matrycowe.
Kucie odbywa się w temp. około 850°C. Ostateczny kształt zarysu wieńca
koła uzyskuje się poprzez obróbkę skrawaniem. Do toczenia kół używane
są specjalne tokarki karuzelowe, służące do obróbki przedmiotów
wielkogabarytowych.
Koła monoblokowe wykonywane są ze stali węglowych przeznaczonych dla
kolejnictwa, np. P58 lub St7P. Stal taka jest po obróbce plastycznej
poddawana wygrzewaniu, nazywanym normalizowaniem. Może być ulepszana
cieplnie. Najczęściej jednak ulepsza się cieplnie tylko wieniec - są to
tzw. koła bezobręczowe typu T.
Wymiary średnicy koła są zawarte w normach branżowych i są
różne w zależności od przeznaczenia i prędkości jazdy. Obecnie koła dla
wagonów do prędkości jazdy 200 km/h mają średnicę 920 mm. Spotykane są
też koła o średnicy 1000 mm i 890 mm.
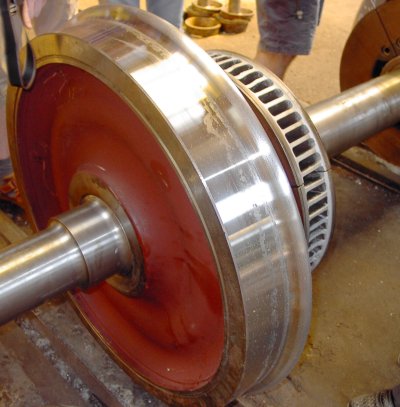
Nowe koło monoblokowe zmontowane w zestaw kołowy
Na powyższym zdjęciu można
zauważyć rowek wycięty w płaszczyźnie czołowej zewnętrznej koła. Służy
on kontroli stanu zużycia powierzchni tocznej. Gdy koło jest zużyte
tak, że powierzchnia toczna dochodzi do rowka, należy koło wymienić na
nowe.
Koła obręczowe
Koła obręczowe składają się z koła bosego,
obręczy i stalwego pierścienia zaciskowego zabezpieczającego obręcz
przed zsunięciem. Koła takie były do niedawna powszechnie stosowane ze
względu na dosyć łatwą i tanią wymianę obręczy po jej zużyciu bez
potrzeby wymiany całego koła. Ponadto cechują się one cichszym biegiem
dzięki zastosowaniu miększej stali normalizowanej na koło bose. Obręcz
jednocześnie mogła być zahartowana, zapewniając dużą odporność zestawu
na działania mechaniczne (zużycie ścierne, rozwalcowanie). Kolejną
zaletą kół obręczowych (składanych) jest możliwość dodatkowego
wyciszenia pojazdu poprzez włożenie materiału amortyzującego,
najczęściej specjalnej gumy, pomiędzy obręcz i koło bose. Nazywane jest
to często zerowym stopniem usprężynowania. Takie rozwiązanie istnieje
np. w popularnym tramwaju typu 105N. Próbowano to także zastosować w
pociągach ICE w celu redukcji hałasu, jednak po wypadku w 1997 roku
wycofano się z tego pomysłu z powodów bezpieczeństwa.
Obręcz koła wykonywana jest przez rozwalcowanie lub kucie
na gorąco fragmentu wlewka z wybitym wewnątrz otworem o średnicy 170
mm. Wlewek nagrzewa się do temperatury około 1200°C, a kucie
przeprowadza się w temp. powyżej 850°C. Materiałem na obręcze
najczęściej jest stal P55A lub P54, ulepszana cieplnie.
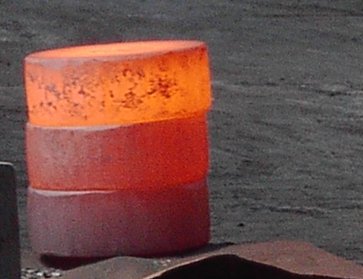
Ucięte wlewki z przebitym otworem, przygotowane do
kucia obręczy
Po obróbce cieplnej
najczęściej toczy się obręcz, wykonuje rowek i podczęcie do włożenia
pierścienia zaciskowego. Pierścień zaciskowy to przecięty w jednym
miejscu okrąg, wykonany ze zwykłej stali, np. St5. Jest on
zawalcowywany w specjalnym rowku z użyciem walcarki w podwyższonej
temperaturze (około 300°C)
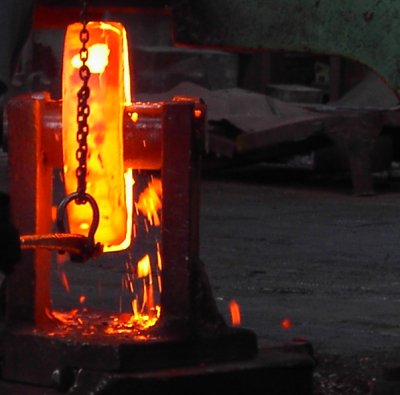
Wykonywanie obręczy przez kucie pierścienia
Obręcz
połączona jest z kołem bosym skurczowo. Części te łączy się w
specjalnym przyrządzie, po uprzednim nagrzaniu obręczy do temp.
300-400°C. W tej temperaturze wkłada się koło bose w obręcz zamocowaną
w uchwycie i studzi się zmontowane koło w spokojnym powietrzu.
Połączenie utrzymywane jest w wyniku istnienia stałego naprężenia
sprężystego w materiale części łączonych.
Montaż zestawów
kołowych
Po zmontowaniu kół następuje końcowy
montaż zestawów kołowych, czyli połączenie kół z osią. Połączenie to
jest w Polsce wykonywane wyłącznie na zimno, poprzez wciśnięcie osi w
piastę koła na specjalnej prasie. Używane są bardzo duże siły
wtłaczania, dochodzące nawet do 7 kN na mm średnicy połączenia.
Podczas operacji wtłaczania wykonywany jest specjalny
wykres, pokazujący zależność siły wtłaczania P od drogi wtłaczania f. Jest to bardzo istotne w
przypadku jakichkolwiek wątpliwości odbiorcy.
Przykładowy wykres
wtłaczania koła na oś
|
|